Литьевая форма в сборе, как правило, имеет в своем составе набор плит, формообразующую, холодоканальную или горячеканальную литниковую систему, систему выталкивания отформованных изделий, систему охлаждения формы, систему выпаров и набор направляющих элементов. Технология изготовления форм может быть сравнена с технологией штампов или печатных плат, подобна им. Современное промышленное производство часто ставит необходимостью интенсифицирование процесса литья пластмасс. Если такая ситуация имеет место быть, то зачастую прибегают к помощи форм длят одновременного производства нескольких изделий, изготавливают и применяют именно их. Такие пресс-формы называют многогнездными (многоместными). Отметим, что число гнезд обычно бывает кратно двум в n-ной степени, например, 2, 4, 8, 16, 32, 64, 128. Однако бывают и формы, имеющие 6, 10, 12, 24. 48, 96 гнезд. Формы, включающие в себя наибольшее количество мест, изготавливают для комплексов, производящих ПЭТ прессформы.
Как правило, проектировка пресс-формы осуществляется для последующего производства какого-либо одного изделия из пластика. Впрочем существуют и так называемые «модульные» формы, предполагающие по своей конструкции сменные компоненты, позволяющие изменять конструкцию изделий или же полностью заменить изделие на другое. Получается, что при таком подходе одна и та же пресс-форма предоставляет возможность производства разных изделий в разное время. Очевидно, что у данной технологии есть не только свои достоинства, но и недостатки, к которым можно отнести трудоемкость операций по периодическому изменению конструкции форм, необходимость более тщательного и частого обслуживания таких форм, небольшой ресурс универсальных форм. В конечном же итоге право выбора вида пресс-формы по данному критерию остается за покупателем продукции такого рода.
Существует и другой путь изготовления различных изделий посредством применения одной литьевой формы. В чем же состоит данный путь? В устройстве формообразующих на различные продукты в одной многогнездной форме. Если применять в ходе производства подобную форму, то можно изготавливать разные изделия, но при этом из одного материала, за один цикл литья. Основная задача проектировщика при этом – правильно сбалансировать литниковую систему для равномерного заполнения всех гнезд такой формы и получения качественной продукции.
При условии относительно простой конструкции и большой площади изделия, иногда для интенсификации литья под давлением прибегают к конструированию так называемых «этажных» форм. Для этих форм характерно наличие двух параллельных плоскостей разъема, при многоместной конструкции они могут вести свою работу на относительно небольших термопластавтоматах. Разумеется, у форм такого плана есть определенные свои недостатки: дорогостоящий горячий канал, увеличенный пакет плит (высота прессформы), что иногда вызывает необходимость применения нестандартных узлов смыкания ТПА. Для качественных литьевых форм характерно выполнение с допуском 0,005 мм. Гарантийный ресурс инструментов от лучших поставщиков исчисляется миллионами литьевых циклов.
Как правило, проектирование пресс-формы состоит из четырех основных этапов. Первый этап подразумевает оценку технологических требований к форме, здесь же производится подробный анализ технологичности деталей изделия. Если возникает такая необходимость, то в конструкцию изделия могут быть внесены изменения. Совместно с этим происходит согласование с заказчиком. На этом же этапе производится разработка трехмерных моделей и чертежей изделия. Второй этап предполагает оптимизацию размещения деталей в оснастке для достижения наибольшей технико-экономической целесообразности.
Следующий этап – третий, предполагает проведение оптимизации конструкции литниковой холодно- или горячеканальной системы и системы охлаждения пресс-формы. Конструкторами используется современное программное обеспечение, предоставляющее возможность в кратчайшие сроки и с высокой точностью выполнять подобные работы. Ну и четвертый этап, последний, состоит в изготовлении комплекта документации на форму, в том числе двумерные чертежи и 3D модели, а также схемы и инструкции по работе с формой, которые понадобятся для осуществления у заказчика правильной эксплуатации.
Предназначение литниковой системы пресс-формы заключается в доставке полимерного материала из материального цилиндра термопластавтомата в формообразующие полости. Выделяется два основных класса литниковых систем – холодноканальные и горячеканальные системы. Если речь идет о первом виде литниковой системы формы, то здесь обогрев литника отсутствует, а при охлаждении отформованной отливки он также охлаждается и выпадает вместе с отливкой при открытии или после открытия формы. На холодоканальные формы установилась существенно более низкая цена, нежели на горячеканальные аналоги. Кромке того, холодоканальные системы надежнее и проще в обслуживании, да и стоимость обслуживания в случае с ними меньше. Однако зачастую все названные достоинства перекрывает наличие одного недостатка – образование после каждого цикла ненужного литника. Масса литника резко растет вверх параллельно с увеличением гнезд в форме, и при производстве множества мелких деталей в одной форме возможно превышение массы собственно готовых деталей массой литника. Но и это еще не все: по причине наличия массивного литника временами происходит увеличение времени цикла, возможно также ухудшение экономических показателей процесса литья. Также по данной причине вероятно возникновение необходимости использования ТПА большего типоразмера с большим номинальным объемом впрыска за цикл. В состав холодной литниковой системы, как правило, входят центральный литник, разводящие литники и впускные литники. Для того, чтобы изделия получались качественными, холодоканальная многоместная система должна быть сбалансирована, а достичь этого не так просто в виду того, что простой геометрической сбалансированности литниковой часто бывает недостаточно.
Использование горячеканальной литниковой системы характеризуется расплавленным состоянием литника. Перед тем, как форма будет запущена в работу, осуществляется разогрев горячеканальной литниковой системы, после же данных действий, в течение всего времени выпуска партий изделий, полимерный материал в литнике поддерживают в вязкотекучем состоянии. Как уже было отмечено в данной статье, горячеканальные системы дороги, сложны конструктивно, сложны в обслуживании. Главным достоинством горячих каналов является отсутствие затвердевших литников, выпадающих вместе с готовыми изделиями при каждом литьевом цикле.
Помимо экономии пластика и отсутствия отходов у горячеканальной системы есть и другие преимущества. Так, в частности, она предоставляется возможность применения ТПА с меньшим объемом впрыска, а также позволяет достичь уменьшения времени пластикации полимера и время охлаждения отливки. Однако следует помнить о такой особенности, как то, что горячеканальные формы требуют более интенсивного охлаждения и больших затрат электроэнергии. Современные формы включают в свой состав нормализованные сопла горячих каналов. Коллекторы же могут быть и специально спроектированы. Все большее применение приобретают так называемые теплопроводящие сопла, не предусматривающие наличия собственных нагревателей, а обогревающиеся за счет горячего коллектора. Материалом для таких сопел служит специальный теплопроводящий сплав бериллиевой бронзы (бериллиевой меди, бериллий латуни). Эта более дешевая, однако устаревшая конструкция, обладает таки недостатками, как сложность регулирования температуры по соплам горячего канала, вредные для здоровья материалы сопел. Отметим, что в ряде стран эти материалы даже запрещены к использованию. Среди систем сброса готовых изделии существует деление на механические и пневматические. В случае особо сложных деталей отливки выемка изделий из формы бывает возможна только в ручную или при помощи робота.
Среди наиболее часто использующихся видов механических выталкивателей можно назвать: выталкивающие плиты, стержневые толкатели, плоские толкатели и трубчатые толкатели. Кроме названных возможно применение и различных нестандартных толкателей. Представленные же могут быть использованы в комплексе, как при одностадийном, так и при многостадийном выталкивании отливок.
Кроме того, что уже было названо, в конструкцию форм для литья пластмасс под давлением входят и такие системы, как: система охлаждения, в состав которой входят множество прямых, кольцевых и специальных каналов для охлаждающей жидкости; система выпоров, предназначение которой состоит в свободном выходе воздуха и формообразующих полостей формы; а также система направляющих и центрующих элементов формы, состоящая из комплекта направляющих втулок и колонок, разного рода зацепов, ползунов, центрующих плит и т. п.
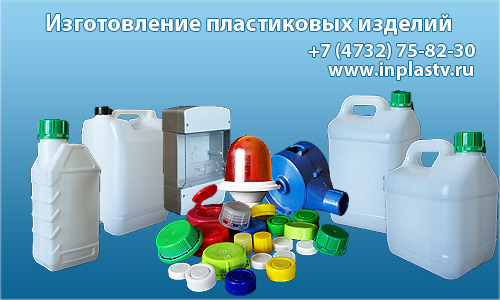
_____________________________________________________________________________
Архив новостей:
20/07/2011
Этапы развития китайского рынка пресс-форм для пластмассовых изделий В 2006 году объем ...19/07/2011
Пресс-формы для пластмассовых изделий: уровень развития и рыночные тенденции В последнее время ...17/07/2011
Пресс-формы для литья пластмасс: виды, элементы, этапы производства Среди всех известных в ...16/07/2011
Пресс-формы для литья пластмасс: виды, элементы, этапы производства Среди всех известных в ...15/06/2011
Основная задача при литье пластмассы под давлением — получение высококачественных изделий при ...12/06/2011
Основная задача при литье пластмассы под давлением — получение высококачественных изделий при ...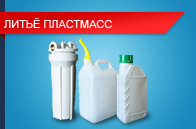
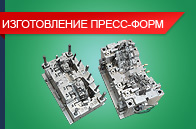
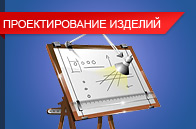