Литье пластмассы под давлением является одни из основных способов переработки полимеров. Этот способ позволяет изготавливать высококачественные изделия из различных пластических материалов с высокой производительностью труда. В настоящее время с помощью литьем пластмассы под давление производят большое количество разнообразных деталей, начиная от пуговиц и упаковочной тары, заканчивая ответственными деталями приборов и оборудования.
Большая часть практических вопросов использования этого способа связана с особенностями течения полимера и изменением его состояния в зависимости от температуры и давления. Расплавы большинства полимеров, применяемых для литья пластмассы под давлением, обладают значительной вязкостью, поэтому при переработке полимеров наблюдается в основном ламинарное течение. Турбулентное течение встречается, как правило. В тех случаях, когда используют большое давление расплава, а впрыск производят через литник небольшого диаметра (точечный литник).
При впрыске в пресс-форму расплавленного полимера тонкий поверхностный слой его застывает, как только соприкасается с металлом стенок формы. Этот застывший слой изолирует от охлаждения текущий поток расплавленной массы. При этом в центре расплав с относительно небольшой потерей давления продвигается до фронта текучести, выходит там на поверхность, прикасается текущей массой к холодной стенке формы и застывает. Это происходит в результате охлаждения горячей пластмассы в холодной пресс- форме, вследствие чего на оболочке верхней поверхности текущего фронта возникают напряжения, которые благоприятствуют равномерной подаче пластмассы при литье под давлением. Оболочка текущего фронта постоянно разрушается и беспрерывно заменяется горячей расплавленной массой текущей за ним.
В процессе подобного течения расплава при литье пластмассы в материале отливаемой детали возникают напряжения сдвига, вызванные ориентацией и объемным сжатием. Применяемые для литья полимеры состоят из длинных пачек цепных молекул, которые в расплавленном состоянии расположены хаотично. Во время заполнения пресс-формы беспорядочное расположение пачек молекул переходит в упорядоченное, так как они ориентируются в направлении течения.
Литье пластмассы под давлением является одни из основных способов переработки полимеров. Этот способ позволяет изготавливать высококачественные изделия из различных пластических материалов с высокой производительностью труда. В настоящее время с помощью литьем пластмассы под давление производят большое количество разнообразных деталей, начиная от пуговиц и упаковочной тары, заканчивая ответственными деталями приборов и оборудования. Большая часть практических вопросов использования этого способа связана с особенностями течения полимера и изменением его состояния в зависимости от температуры и давления. Расплавы большинства полимеров, применяемых для литья пластмассы под давлением, обладают значительной вязкостью, поэтому при переработке полимеров наблюдается в основном ламинарное течение. Турбулентное течение встречается, как правило. В тех случаях, когда используют большое давление расплава, а впрыск производят через литник небольшого диаметра (точечный литник).
При впрыске в пресс-форму расплавленного полимера тонкий поверхностный слой его застывает, как только соприкасается с металлом стенок формы. Этот застывший слой изолирует от охлаждения текущий поток расплавленной массы. При этом в центре расплав с относительно небольшой потерей давления продвигается до фронта текучести, выходит там на поверхность, прикасается текущей массой к холодной стенке формы и застывает. Это происходит в результате охлаждения горячей пластмассы в холодной пресс- форме, вследствие чего на оболочке верхней поверхности текущего фронта возникают напряжения, которые благоприятствуют равномерной подаче пластмассы при литье под давлением. Оболочка текущего фронта постоянно разрушается и беспрерывно заменяется горячей расплавленной массой текущей за ним.В процессе подобного течения расплава при литье пластмассы в материале отливаемой детали возникают напряжения сдвига, вызванные ориентацией и объемным сжатием. Применяемые для литья полимеры состоят из длинных пачек цепных молекул, которые в расплавленном состоянии расположены хаотично. Во время заполнения пресс-формы беспорядочное расположение пачек молекул переходит в упорядоченное, так как они ориентируются в направлении течения.
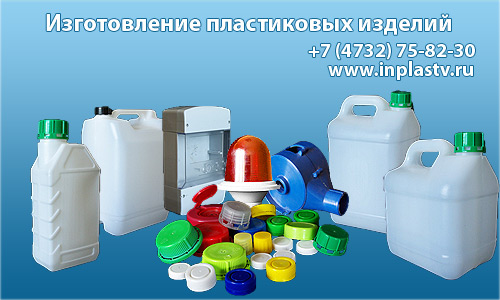
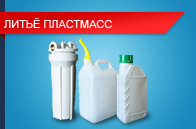
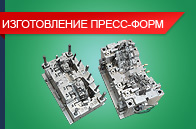
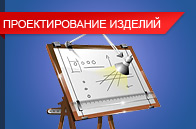